Pest Control is the process of managing pests to preserve property and protect people and animals from harm. It includes preventive, non chemical, biological and, when necessary, chemical methods.
Avoiding pests is a great way to preserve the value of your home. Non chemical prevention methods are usually enough, but if not, there are many products that have low risk to humans and pets when used correctly. Contact Pest Control Braintree now!
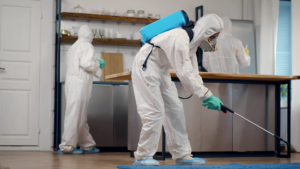
Preventive pest control is the best way to reduce the need for more drastic and costly reactive treatment. It involves an understanding of the pest’s life cycle and behavior, routine inspections, and prompt use of preventive measures.
Some of the most important preventive steps involve eliminating the pests’ food, water, and shelter sources. This can be done by storing foods in tightly sealed containers, removing garbage regularly, and reducing clutter around buildings. In addition, removing or patching holes in walls and around doors helps keep rodents and other pests out. In museum storage and display areas, creating sanitary perimeters on floors through organized layout of shelving and cabinets can decrease the labor involved in inspecting these areas and increasing the success rate of traps and other detection methods.
Other prevention steps can include preventing insect infestations by destroying egg masses, removing larvae from nests, and using pest-repelling plants such as rosemary. In addition, regular vacuuming can help remove carpet beetles and cockroaches before they breed and become a nuisance.
Many people have a knee-jerk reaction to any pest sighting, reaching for the spray bottle of pesticide. While it is often necessary to control some pests, this should always be a last resort. Some pesticides are extremely toxic and should only be used in accordance with the manufacturer’s instructions and safety warnings. In most cases, there are less toxic alternatives, such as baits and traps, that can be just as effective as traditional chemical controls.
It is also important to understand that there are natural forces that affect all organisms, including pests. These can influence pest populations, causing them to rise and fall. For example, cooler temperatures and lower relative humidity can slow the progress of an infestation. Understanding this process can aid in pest control and help to predict how a building might be affected by changes in the environment. In addition, some pests are migratory or cyclical and may require occasional or sporadic control. For example, wood rot and dry rodent droppings can cause damage and health hazards. Occasionally treating the area with wood preservatives or rust inhibitors can be useful in preventing these problems from occurring.
Suppression
Pests are organisms that damage, devalue or destroy crops, landscape plants, turfgrass and ornamental trees, shrubs and flowers. They also disturb terrestrial and aquatic ecosystems, compete with beneficial species and displace native species. The goal of pest control is to reduce pest populations below damaging or intolerable levels.
Suppression methods include a variety of cultural, mechanical, chemical and biological controls. They are used in conjunction with prevention methods to achieve desired results while considering health, the environment and economic feasibility.
Cultural pest control methods aim to change or modify pest habits and/or habitats to prevent or limit the spread of unwanted organisms. These techniques may involve removing or changing physical barriers, introducing or conserving natural enemies of pests, establishing refuges and/or altering environmental factors.
For example, to reduce the number of aphids in a vegetable garden, growers can use floating row covers or nematodes to keep these insects from accessing the plants. Gardeners can plant aphid-resistant varieties of vegetables, shrubs and flowers to limit their numbers.
Many pests have a zero tolerance threshold and cannot be allowed to be present in certain environments, such as restaurants and grocery stores due to health and food safety issues. Eradication is the objective in these situations.
The most common method of controlling aphids is to introduce or conserve parasitoids that kill them. These natural enemies are tiny wasps, flies, beetles and other insects that feed on the aphids. Some are available commercially, such as the wasp Encarsia formosa that kills greenhouse whitefly.
Mechanical and physical control methods involve cutting, crushing, burying, heating or cooling, excluding or imposing barriers, applying heat or light, or physically disturbing pests to alter their behavior or interfere with their life cycles. Examples include window screens for keeping pests out of homes, tulle netting for preventing cutworms from attacking tomato plants, or plastic mulches, row covers and tarping for many horticultural crops.
Chemical controls utilize a variety of pesticides and herbicides to kill or control pests. Some of these chemicals are sprayed directly onto or into the pest, while others are absorbed by the plant and killed internally. Increasingly, growers are seeking alternatives to toxic pesticides. Microbial pesticides use engineered microorganisms – bacteria, viruses and fungi – to kill pests by infecting them with disease. This method works best when soil conditions are ideal, such as moist or irrigated soil and cool temperatures.
Eradication
Pest control is the process of eliminating or managing unwanted creatures, such as rodents, cockroaches, ants, bed bugs, and birds. These organisms are not only a nuisance to humans but can cause serious health issues and property damage. Pest control can be achieved through a variety of methods, including physical trapping, killing, or controlling their populations.
The ultimate goal of pest control is to eradicate them entirely. However, eradication is an ambitious undertaking, and it requires significant financial and human resources. It also involves balancing private and social benefits, short-term and long-term costs, and local versus international net benefits. In addition, it is important to understand the limits of current cost-benefit analyses, which tend to underestimate the costs and overestimate the benefits of eradication.
One way to evaluate the costs and benefits of a pest control program is to compare it with the best alternative. This can be done by projecting future infection rates and vaccination costs, assigning values to them, and discounting them. The result is a sum that represents the cost of eradication and the net benefit to society.
Biological pest control uses natural enemies to reduce the population of unwanted species. These organisms may be predators, parasites, or disease agents that occur naturally in an ecosystem. Some of these organisms, such as the nematode Steinernema carpocapsae, are beneficial to plants and can be used in agricultural settings to manage pest infestations.
Chemical pest control includes the use of poisonous substances that kill or injure the organisms. These substances are often called pesticides and must be used only by qualified professionals because of their danger to human beings, animals, and the environment.
A good pest control program should start with a thorough inspection. The exterminator will look for signs of pests, locate nests or entry points, and assess the extent of the problem. They will then recommend the appropriate treatment options. This will usually involve setting traps and baits. These should be placed in areas where the pests are most likely to appear. These are most likely to be around food sources such as garbage cans and pet food dishes.
Treatment
Pest control includes strategies for dealing with rodents, birds, insects and other organisms that share the same habitat with humans and destroy or spoil our food, property or possessions. A range of techniques can be used to discourage or eliminate pests, including exclusion, quarantine, repulsion, trapping and chemical controls.
When preventive measures fail, chemical pest control steps in to deal with severe infestations or insect populations that have reached harmful levels. There are a wide range of chemical products available, including liquids, powders and aerosols. Choosing the right product for the situation is critical. The best choice will minimize the risks to human health and the environment. In order to minimize exposure, sprays should generally only be applied in out-of-the-way places like along skirting boards or under floorboards. Care should also be taken when using baits, as some contain hazardous materials that could contaminate food or water supplies.
It is important to identify the pest accurately before any treatment. It is common to mistake some pests for others, especially when they are similar in appearance or behaviour. This can lead to unnecessary risk of harm to people and pets, as well as damage to the environment and property. A trained technician can help to reduce this problem by conducting a thorough inspection and identifying the pest species correctly.
Other factors can affect pest numbers, such as the availability of food, water and shelter. In addition, environmental features such as mountains or large bodies of water restrict the spread of some pests. Some natural pest control methods can also be used, such as weeding and the use of plant growth regulators.
A wide range of pests cause problems in urban and rural environments. Some have a repulsive or grotesque appearance, such as silverfish and earwigs, while others bite or sting, as in the case of bees, wasps, cluster flies and mud dauber wasps. Others damage or stain property, such as rats, mice and cockroaches. Some pests are carriers of dangerous bacteria, such as cockroaches and fleas, while others can spread viruses, such as those carried by ants and termites.