You can find a good concrete contractor by doing some research. Look for reviews and feedback from previous customers. The length of time a contractor has been in business also says a lot. It indicates that they have been providing quality services for a long time.
Commercial Concrete Contractors Dallas TX projects entail a lot of technical details that must be communicated to the clients. This requires a contractor to have the right qualifications.
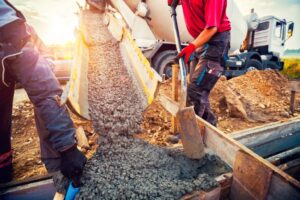
Concrete contractors are responsible for building a wide range of projects. Their work includes everything from residential driveways to commercial and road construction. To be successful, they need to have a combination of experience and qualifications. These include education, licensing, and a strong reputation. In addition, they need to have business skills to run their company. This includes balancing job site experience with office work and managing paperwork. This allows them to develop good relationships with employees, subcontractors, and clients.
The first qualification you must meet to become a concrete contractor is an associate’s or bachelor’s degree in civil engineering or a related subject. You should also take courses in mathematics, business, and concrete design. This will give you a solid background in the industry and help you understand complex concepts and procedures. Depending on the type of project you want to undertake, you may also need to complete specific training programs to ensure that your final product meets all requirements.
Before you hire a concrete contractor, make sure to ask them for references from previous customers. This will help you gauge their reliability and professionalism. Also, check the reputation of the company online. You should avoid hiring a contractor with negative reviews, which may indicate negligence.
A reliable concrete contractor will have a good reputation in the industry and provide high-quality service. They will also be licensed by local authorities to perform concrete works. Moreover, they will have an excellent compliance record with building codes and regulations. This is crucial for ensuring the safety and quality of the work.
Moreover, the contractor should have a solid relationship with suppliers who deliver quality concrete on time. They should also arrange a delivery service to ease the logistics of producing large amounts of concrete. This will save them time and energy, especially when working on large-scale projects.
A reputable concrete contractor will have a solid relationship with the supplier and have access to a wide range of materials. They will also be able to advise on handling certain situations. They will also have a good understanding of the physics and dynamics of concrete. This will allow them to provide accurate estimates and prevent delays in the project.
Whether they work on residential, commercial, or industrial projects, concrete contractors have the knowledge and experience to provide high-quality concrete structures. They understand the properties of various concrete mixes and can advise on how to use them in different types of construction. They are also familiar with building codes and safety standards in their work areas.
A good contractor will have a large portfolio of past projects and be able to provide references. These references can help you determine if the concrete professional is a good fit for your project. It would be best if you got an honest, unbiased opinion of the contractor’s work from these references. In addition, you can check online reviews to see what other people say about the contractor’s work.
In addition to experience, a concrete contractor should have good working relationships with local suppliers. This can help them get the right mix for a particular job and may save you money in the long run. Good supplier relations will also help you avoid costly mistakes and delays.
There was a time when concrete contractors prepared the concrete they needed for a project themselves. However, with ready-mix plants now available in most areas, many can do this without doing this. This frees up their time to focus on other aspects of the job and ensure that the final output matches the client’s ideas and preferences.
Concrete contractors typically specialize in a certain business area, such as commercial, residential, or road construction. They may also choose to focus on a particular type of project, such as foundations or patios. In addition, a concrete contractor will need to have excellent office skills and be able to manage paperwork and financial issues. They must also communicate well with clients, general contractors, and other employees. Finally, they should be able to set reasonable deadlines and follow through on their promises. You should look for a different contractor if they don’t deliver on their promises.
Concrete is a construction material that can be used in various ways. It can be cast in slabs for roadways, as partition walls for buildings and structures, or even as tiles that make floors. Depending on the type of work, it is important to have a valid license before beginning any project. This ensures that you can perform your job properly and legally.
Becoming a licensed concrete contractor requires completing an apprenticeship program and receiving instruction from a qualified supervisor. In addition, you must also obtain a certificate from the American Concrete Institute. This shows that you are knowledgeable about the construction and testing of concrete structures. This can help you build a successful and profitable business.
Licensed concrete contractors can work on various residential, commercial, and road construction projects. The main task is constructing concrete structures to meet clients’ preferences and ideas. To do this, the contractor needs to be able to read blueprints and understand engineering drawings. The contractor must also know how to select the correct materials and equipment for the project. They should also have good interpersonal skills to develop positive relationships with the general contractor and clients.
Aside from constructing concrete, a licensed concrete contractor can also repair and maintain existing structures. This is often done for offices, schools, and other commercial buildings. The contractor must be able to work closely with architects and engineers to ensure that the concrete meets all the necessary specifications and regulations.
Finding reliable suppliers is one of the most important factors when becoming a concrete contractor. These suppliers should be able to provide pre-mixed concrete, which can save time and money. Additionally, they should be able to deliver the concrete on time and in the proper condition.
Another thing to remember is that licensing requirements vary from state to state. You should research the requirements for your specific state before getting started. Contractor Training Center can help you through the entire process, and they have experts ready to answer any questions you may have.
Concrete contractors take on a lot of risks in their line of work, and the job sites can be dangerous for employees and third parties. The business also requires a lot of heavy equipment and materials, which can be expensive to repair or replace in an accident or natural disaster. Whether you’re starting a new construction project or have been in the business for years, insurance can help you cover losses without bankrupting your company.
The most essential type of business insurance for concrete contractors is general liability. This policy protects your business when your work damages a client’s property. It also covers medical expenses and other legal fees in the event of an injury caused by your business. A business owner policy (BOP) often includes general liability, which bundles public and commercial property insurance for a discount.
Workers’ compensation insurance is another necessary type of coverage for concrete contractors. This policy covers medical costs and lost wages for workers who are injured on the job. It’s a requirement for most businesses, and many clients will only hire an insured concrete contractor.
Business auto insurance is also a must-have for concrete contractors, as it protects against physical damage or liability claims resulting from using company vehicles. Many states have specific requirements for auto coverage, and it’s generally bundled with general liability and workers’ compensation insurance in a BOP.
Commercial property insurance is a must-have for concrete contractors, and it covers the company’s building and any machinery or equipment stored inside. This coverage protects your business from common perils, including fire, windstorms, and vandalism.
The cost of insurance for concrete contractors depends on several factors, including the size of the business, its location, and the number of employees. Additionally, the amount of work done and the risk of accidents and injuries can also affect the cost of premiums. However, reducing risks and improving safety can minimize the impact on your insurance costs.